Integrating Automation and AI: What is Alpha X's Approach to Factory Digitalization in Southeast...
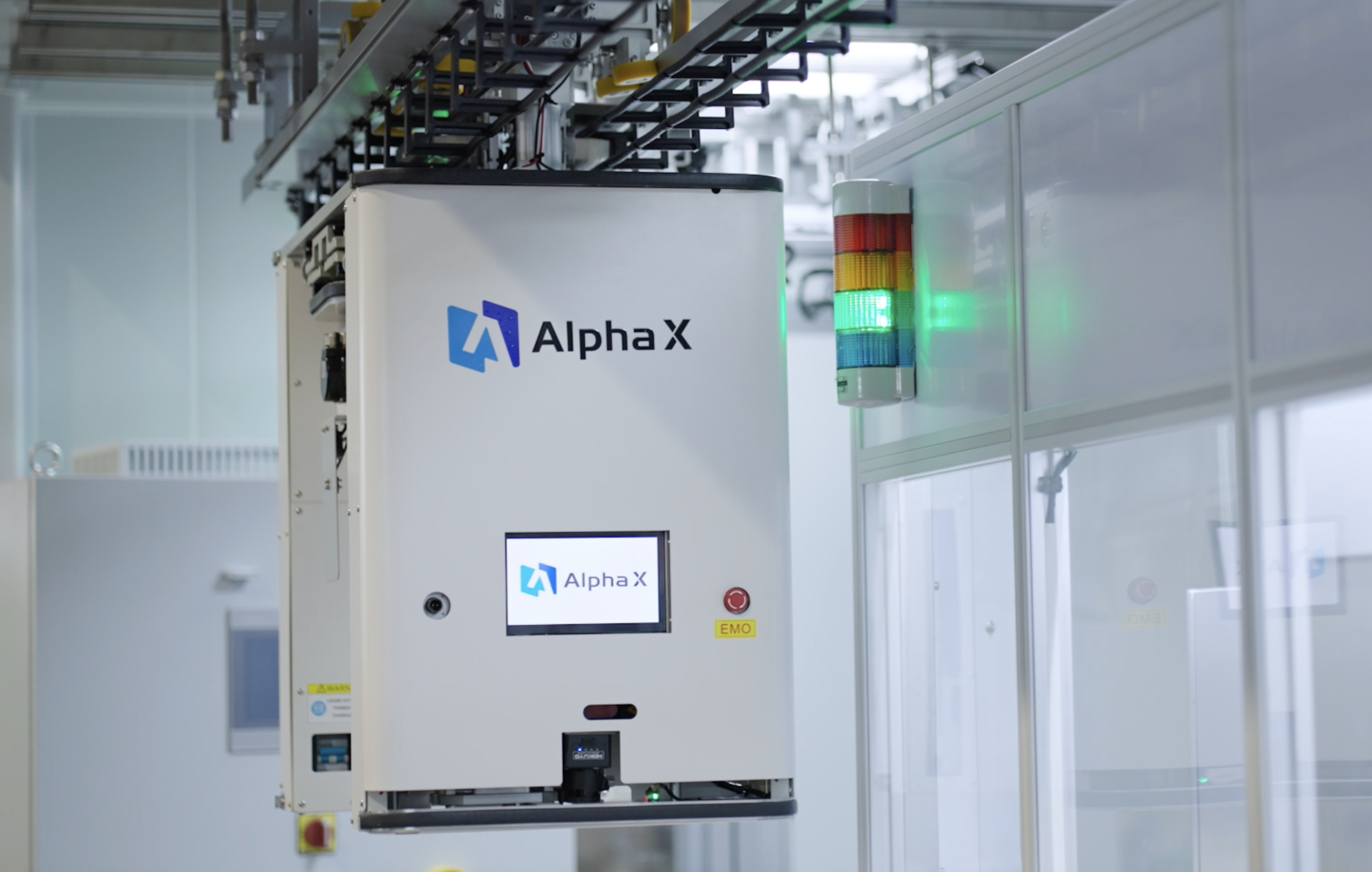
Alpha X is on an ambitious path of rapid growth, aiming to establish a firm presence in the high-tech manufacturing sector, especially for semiconductor. This year, we’re focusing on scaling our team and expanding our technology solutions to interface with more clients. By integrating advanced automation technology, we are setting ourselves apart as a significant player in logistics automation for semiconductor manufacturing.
Alpha X OHT System: Core Functionalities and Advantages
Our Overhead Hoist Transport (OHT) system is a core part of Alpha X’s Automated Material Handling System (AMHS), specifically designed for clean room environments typical of semiconductor fabs. The OHT system automates the transport of carriers containing silicon wafers , which must be handled with extreme care and precision. Here’s a breakdown of the OHT’s core functionalities:
- Overhead Rail Infrastructure: By utilizing an overhead rail system, our OHT frees up valuable floor space in semiconductor fabs, allowing for optimized tool storage and enhanced productivity. This also helps maintain cleanroom standards by minimizing ground-level contamination.
- Automated Loading and Unloading: The OHT system automates wafer carrier handling, eliminating the risks of human error, contamination, and mishandling. This consistent, automated workflow reduces delays in production lines, ensuring that fabs maintain high productivity and quality standards.
- Overhead Buffer Shelves: These shelves serve as temporary storage, enabling operational flexibility by holding materials without disrupting downstream processes. This is especially useful in high-throughput environments, preventing bottlenecks and streamlining the workflow.
- Dynamic Rerouting: Unlike systems that follow fixed paths, our OHT system’s dynamic rerouting feature enables it to bypass congested areas and adapt to real-time changes in production needs. This capability optimizes workflow and reduces the energy consumed by unnecessary movement.
Key Benefits of the Alpha X OHT System
The Alpha X OHT system not only optimizes logistics within wafer fabs but also aligns with sustainability and energy efficiency goals:
- Intelligent Handling with Advanced Automation
The Alpha X OHT system elevates semiconductor logistics with its intelligent, automation-driven transport capabilities. Fully integrated with Manufacturing Execution Systems (MES) and Material Control Systems (MCS), the system enables seamless, automated wafer transport with unparalleled stability and precision. Through intelligent dispatching, Alpha X proactively assigns transport tasks, ensuring fast and precise handling, with speeds of up to 5.3 m/s. This real-time task assignment helps optimize wafer throughput in high-volume fab environments, eliminating human error and significantly enhancing transport accuracy. The automated system also ensures stable movement of sensitive wafers, which is critical in semiconductor manufacturing. - High-Speed and Efficient Transport
The Alpha X OHT system is engineered for maximum throughput, achieving straight travel speeds of 5.3 m/s (without FOUP) and 1.9 m/s hoist speeds (empty). These speeds, combined with acceleration of up to 2.0 m/s² and deceleration of up to 3.0 m/s², make Alpha X highly efficient at reducing cycle times while maintaining precise and reliable handling, even under demanding fab conditions. Whether handling 12" FOUP, 6"/8" SMIF Pods, or magazines, Alpha X is designed to move wafers quickly without compromising safety, stability, or cleanliness. - Cleaner, Safer, and Maintenance-Free Transport
One of the critical challenges in semiconductor fabs is maintaining the stringent cleanliness standards required for wafer handling. Alpha X addresses this by integrating contactless power supply systems (HID), which reduce the physical footprint of traditional transport systems and minimize contamination risks. The maintenance-free nature of the wireless system not only meets Class 100 cleanliness standards but also optimizes space utilization within cleanroom environments. This makes the system cleaner, safer, and more efficient, offering a low-vibration operation (<0.5 G) to ensure wafer integrity during transport. - Real-Time Adaptive Rerouting for Optimal Efficiency
Alpha X's advanced routing algorithms allow the system to adapt in real-time to changing production conditions. By analyzing real-time data from the MES and MCS, Alpha X dynamically reroutes transport paths to avoid congestion, reduce idle times, and enhance throughput. This predictive rerouting capability ensures that Alpha X stays ahead of potential bottlenecks, aligning transport tasks with the real-time needs of the production schedule. The result is a continuous, efficient flow of materials, reducing delays, minimizing transport distances, and lowering overall energy consumption—making Alpha X an environmentally sustainable solution for wafer transport. - Superior Positioning Accuracy and Stability
Alpha X offers ±1 mm positioning accuracy, ensuring that wafers are transported with the highest precision. This minimizes handling errors and prevents contamination or damage, which is critical in semiconductor manufacturing. With a robust hoisting mechanism that supports 1.9 m/s speeds (empty) and 3.0 m/s² acceleration for unloaded carriers, Alpha X maintains smooth vertical transport even when handling delicate or heavy loads, offering optimal control over movement throughout the fab. - Enhancing Production Efficiency and Yield
Alpha X significantly enhances production flexibility by reducing bottlenecks between processing stages. By streamlining wafer movement and minimizing waiting times, Alpha X contributes to an increase in overall fab efficiency and can help improve product yield. (Please note: Performance improvements, such as increases in fab efficiency and yield, may vary depending on individual fab conditions, processes, and integration levels. Results may differ across different fab environments and use cases.) Furthermore, Alpha X’s automated handling system significantly reduces the risk of wafer damage caused by human errors—cutting fragmentation rates by up to 99%. This ensures that each wafer is moved with maximum care and precision, preserving its integrity and minimizing costly defects. This results in fewer defects and higher yield, driving cost savings and improving overall fab productivity. - Scalability and Future-Proof Integration
Alpha X is designed with scalability in mind, ensuring that as your fab grows and evolves, the system can seamlessly adapt to changing production demands. Whether you're dealing with larger wafer sizes, more complex production processes, or expanding fab capacities, Alpha X’s modular design and integrated intelligence allow it to scale efficiently without requiring major overhauls. The ability to integrate with MES and MCS systems ensures that Alpha X can continually optimize its transport tasks, maintaining performance while meeting future semiconductor production challenges. - Compact Design with Optimized Space Utilization
With a compact footprint ranging from 780 mm to 1050 mm in width and 450 mm to 650 mm in depth, Alpha X maximizes fab space utilization while maintaining the high-performance capabilities required for semiconductor handling. With a bottom/ceiling clearance of 1100 mm (for applicable models), Alpha X is well-suited for fabs with lower ceiling heights, enabling seamless integration into cleanroom environments. This feature helps optimize space within critical clean areas, enhancing workflow efficiency while maintaining the necessary cleanliness standards.
Industry Applications and Partnership Potential
Our primary focus with the OHT system is on the semiconductor industry, particularly in wafer fabs, from front-end to back-end processes, including advanced packaging. Alpha X’s solutions cater to both front-end and back-end processes, making us a valuable partner for companies that require flexibility across different stages of production. For example, with our dual-capability system, companies like Infineon can streamline their logistics using a single vendor for both front-end and back-end processes, ensuring a more cohesive and integrated manufacturing experience.
Distinct Advantages in the Market
Alpha X differentiates itself from competitors by offering comprehensive, AI-powered automation for logistics. With our Real-Time Dispatch (RTD) feature and seamless integration with other software systems, we provide an adaptable solution that allows clients to continue using their existing systems without disruption. Our open integration approach gives clients the flexibility they need to optimize logistics without being locked into a single system, setting us apart from other OHT suppliers.
Future Prospects in Logistics Automation
Looking ahead, logistics automation is set to play a pivotal role in semiconductor fabs as they increase production demands. In the coming years, clients will rely more on real-time data for decision-making and AI-driven automation to maintain 24/7 production efficiency. This trend will also open new opportunities to upskill the workforce, enabling workers to focus on strategic decision-making rather than data collection.
At Alpha X, we’re ready to meet these future demands, combining robust logistics systems with the power of AI and machine learning. As the industry evolves, our goal remains to empower semiconductor manufacturers with reliable, scalable, and intelligent automation solutions.
As we look toward an innovative future, Alpha X is positioned to be a trusted partner in semiconductor manufacturing, ready to support our clients with tailored, high-performance logistics solutions that push the boundaries of efficiency and precision.